Sustainable Hotel Brand Prototype
Europe
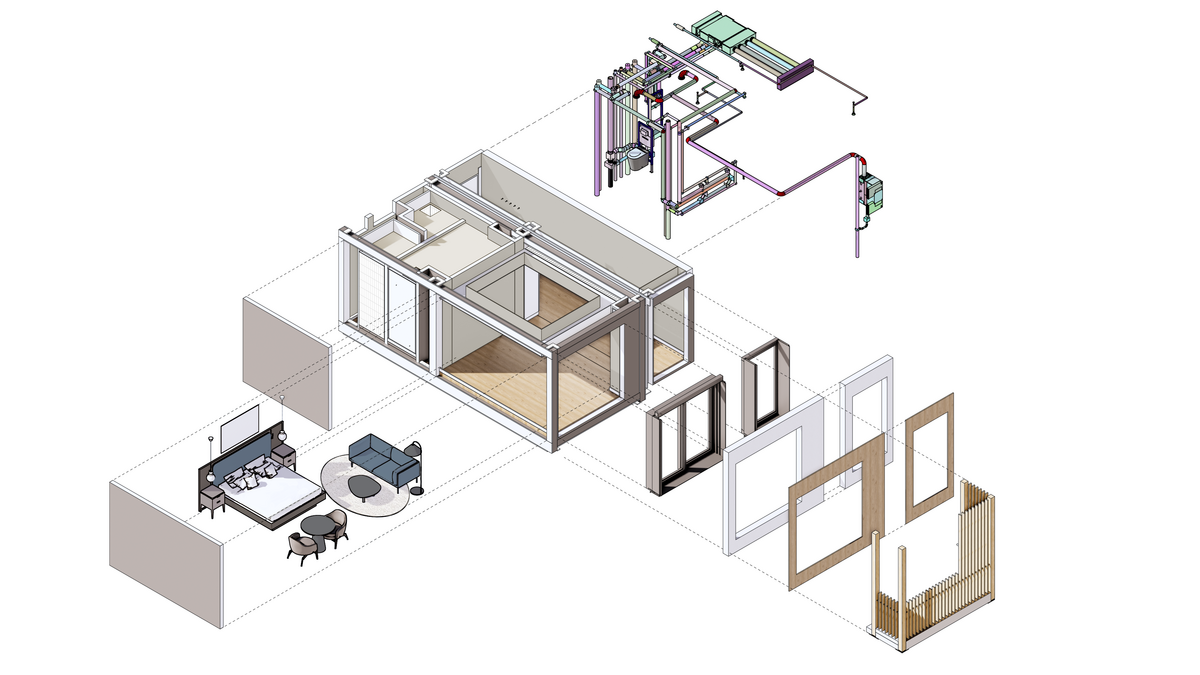
The most sustainable hotel in the world
Type
Brand prototype
Client
Implenia & Rubus Development
Status
On the drawing board
In a world challenged by climate change, finite resources and an increasing focus on personal health and well-being, we are working to create places that have a positive impact on people and the natural environment, whilst also ensuring that the building and operations are carbon-neutral, energy-efficient and circular.
We were approached in the summer of 2021 to work as a part of a research-focused collaborative and multinational design team to develop from first principles a truly sustainable hotel brand roll-out design, committed aesthetically and technically to environmental sustainability. Our team has essentially “started from scratch” by looking closely at design, technical and construction options for any opportunities in operational efficiency gains, waste reduction and future-proofing of the building by scrutinising the life of the building as a whole.
Three distinct 'green hospitality' brands have been developed for the Operator, with the aim of being rolled out across central Europe. Each of the brand designs has a systematic approach which is then readily modifiable to suit local climatic, aesthetic and cultural conditions. The result will be a sustainable and standardised build-system with locality and individuality built in at its heart.
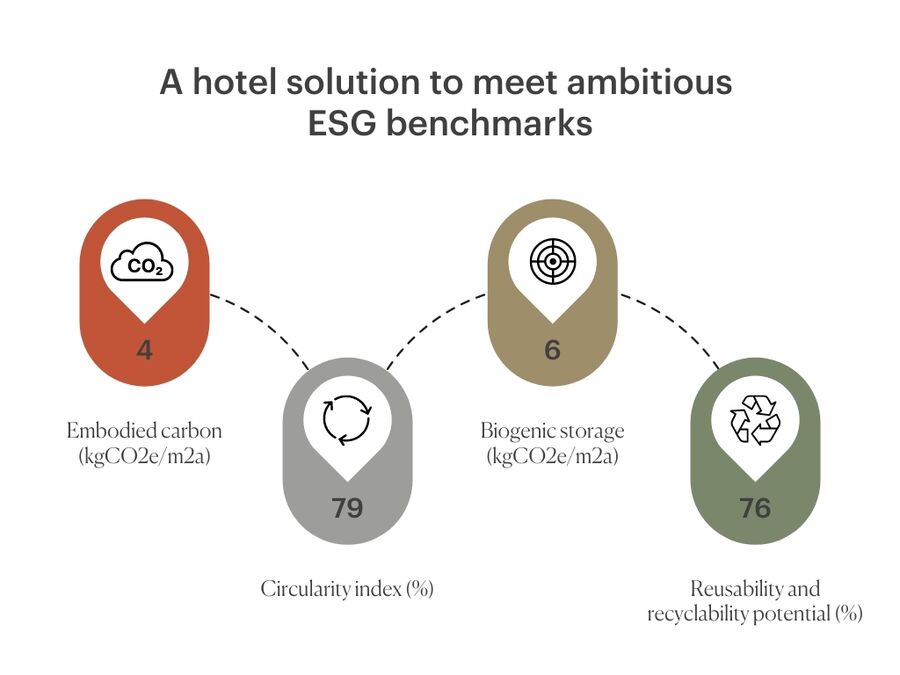
Tangible ecological and economic benefits
• This sustainable brand prototype is optimised for flexibility in use, renewable materials, the separability of modules, elements and material layers and thus a high degree of reusability
• The circularity index of a standard room is 79%, reaching a reusability and recyclability potential of 76% of all materials
• A standard room module reaches an embodied carbon value of 4 kg CO2e/m2a and consists thanks to its timber structure of 35% renewable materials
• With an input of 13.4 m3 of timber the biogenic storage capacity (CO2-sink) of standard room reaches 8’180 kg CO2e (5.8 kgCO2e/m2a). This corresponds to around 9 flights from Zurich to New York
• A 30% lower construction weight of timber leads to a lower concrete and steel input on the level of the foundation and basement
• It can easily compete with ambitious sustainability benchmarks on the level of comfort, CO2, circularity and hazardous substances
Our architectural concept introduces enhanced space-usage flexibility, flow, and explores a strong visual connection between the interior and exterior space.
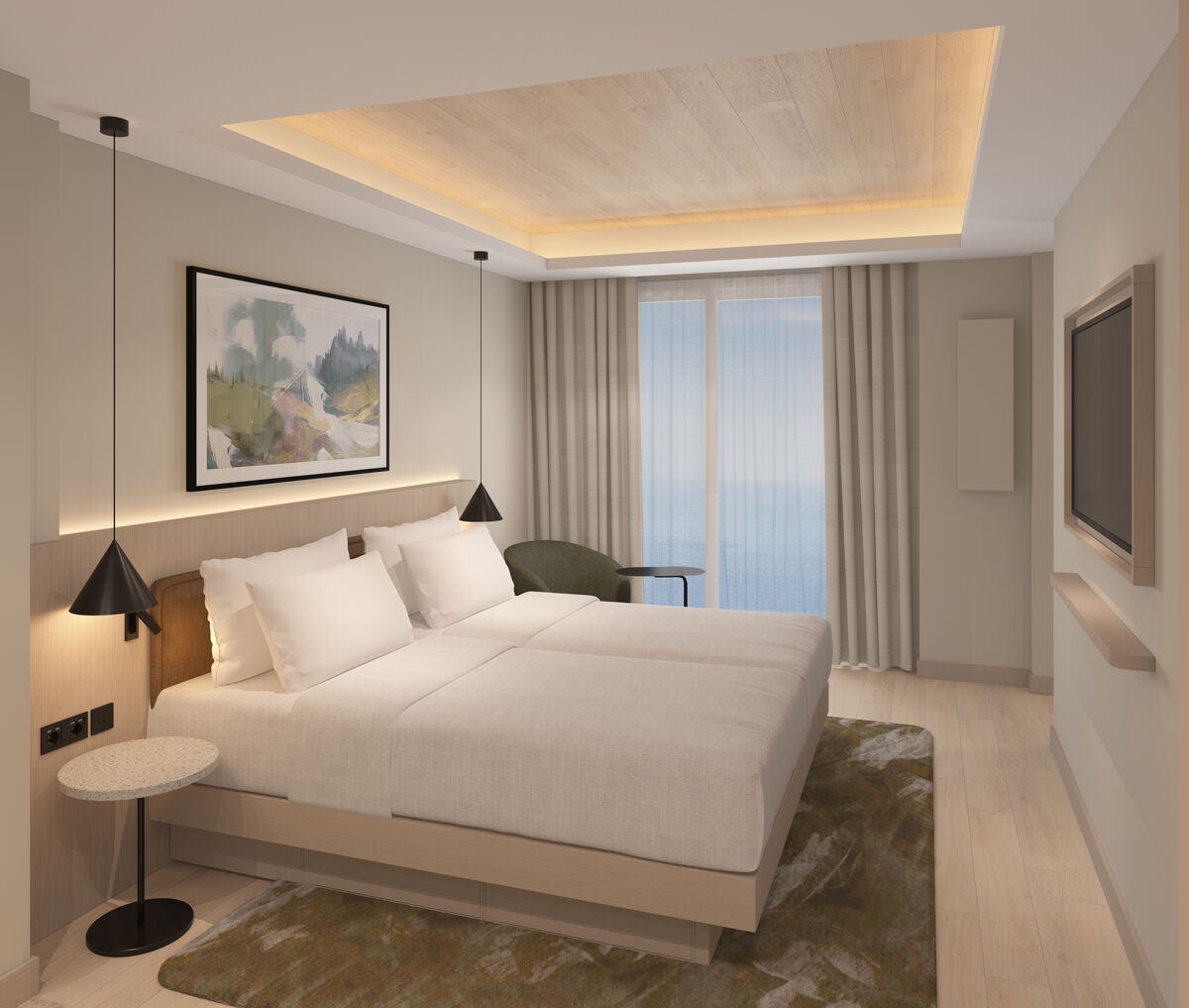
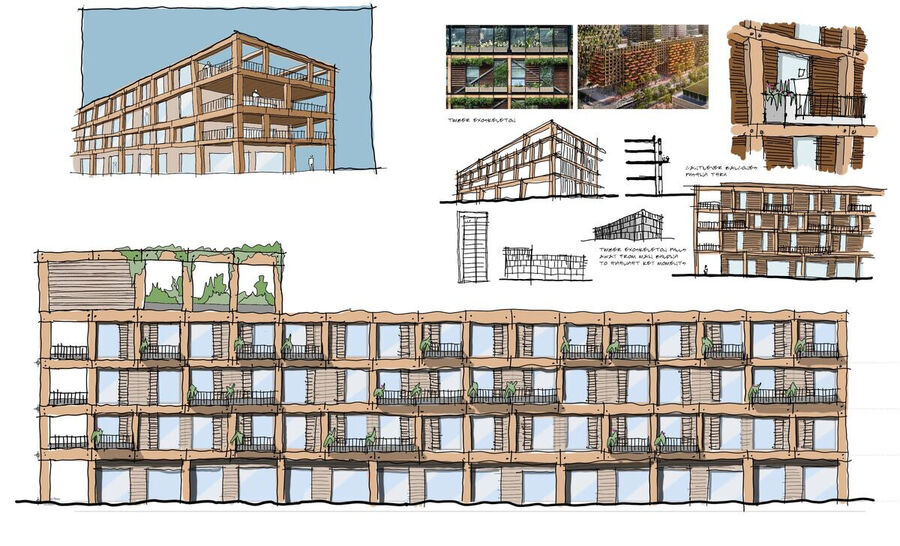
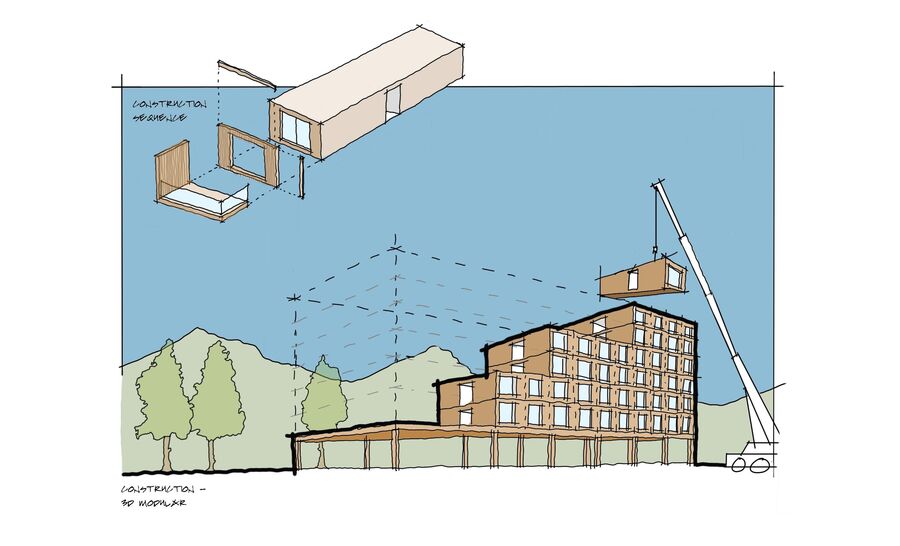
Designed with people, natural resources, and profitability in mind.
Investors
• Short time to market, steady returns and long-term gains • Value stability and appreciation • Green funding accessibility, attractive loans and tax incentives • Risk reduction (ESG, flexibility, operational efficiency, life cycle costs) • Flexibility in use and possibility of repurposing • Cost transparency and data availability
Operators
• Profitability and high occupancy • Operational efficiency • Energy efficiency via renewable resources, energy saving and storage • Flexibility in space usage • Low building maintenance • Cost transparency and data availability • Continuous improvement of performance • Opportunities for additional revenue • Attracting and retaining employees • Strong and reliable partners
Guests
• Wellbeing • Individualisation • Lifestyle upgrade • Authentic experiences • Sustainable travel and stay without restrictions
Improved quality, sustainability, cost and schedule reliability through modular construction and renewable materials.
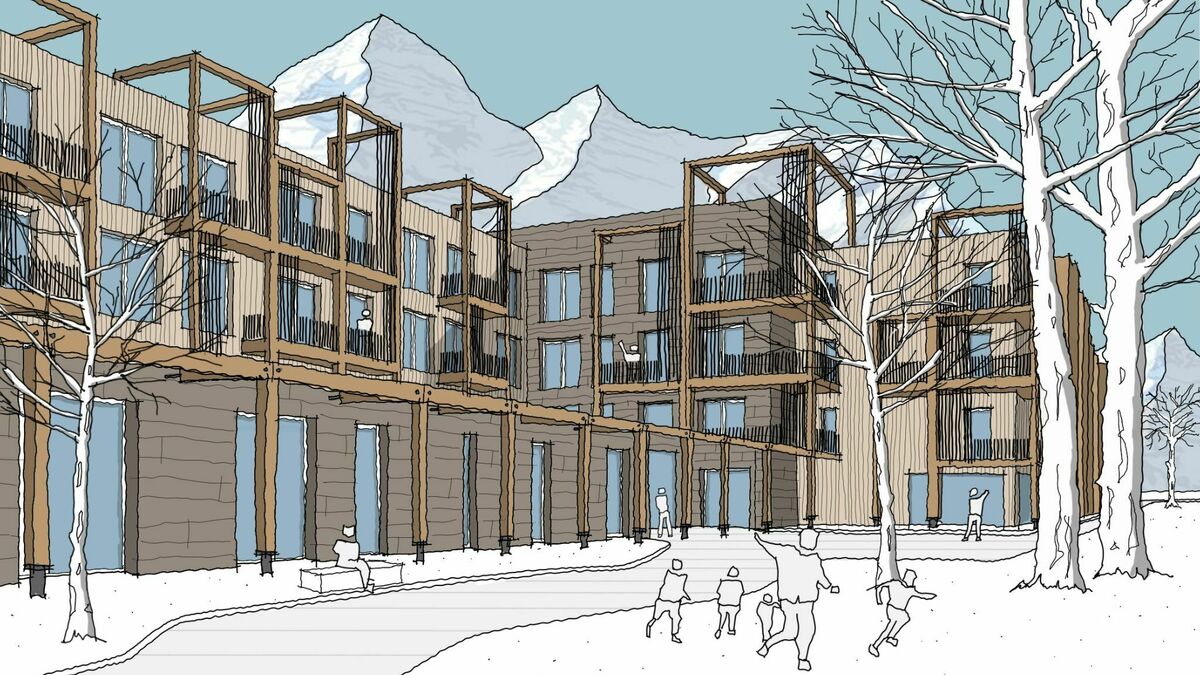
Predictable costs
Up to 80% of the hotel is configured and prefabricated from repetitive room elements, enabling accurate cost estimation. Standardised production allows for bulk purchasing of materials, resulting in lower unit prices and reduced recurring costs in future projects.
Expedited construction timelines
Modular construction significantly shortens the construction phase, by up to 50% - most of the work is completed in a controlled factory environment, while sitework and foundations are simultaneously prepared on-site, leading to faster hotel openings and a quicker return on investment.
Enhanced quality assurance
Critical phases of construction are carried out in a controlled factory environment, ensuring higher product quality and consistency. Reduced waste and improved waste management practices contribute to environmental sustainability compared to traditional on-site construction methods.
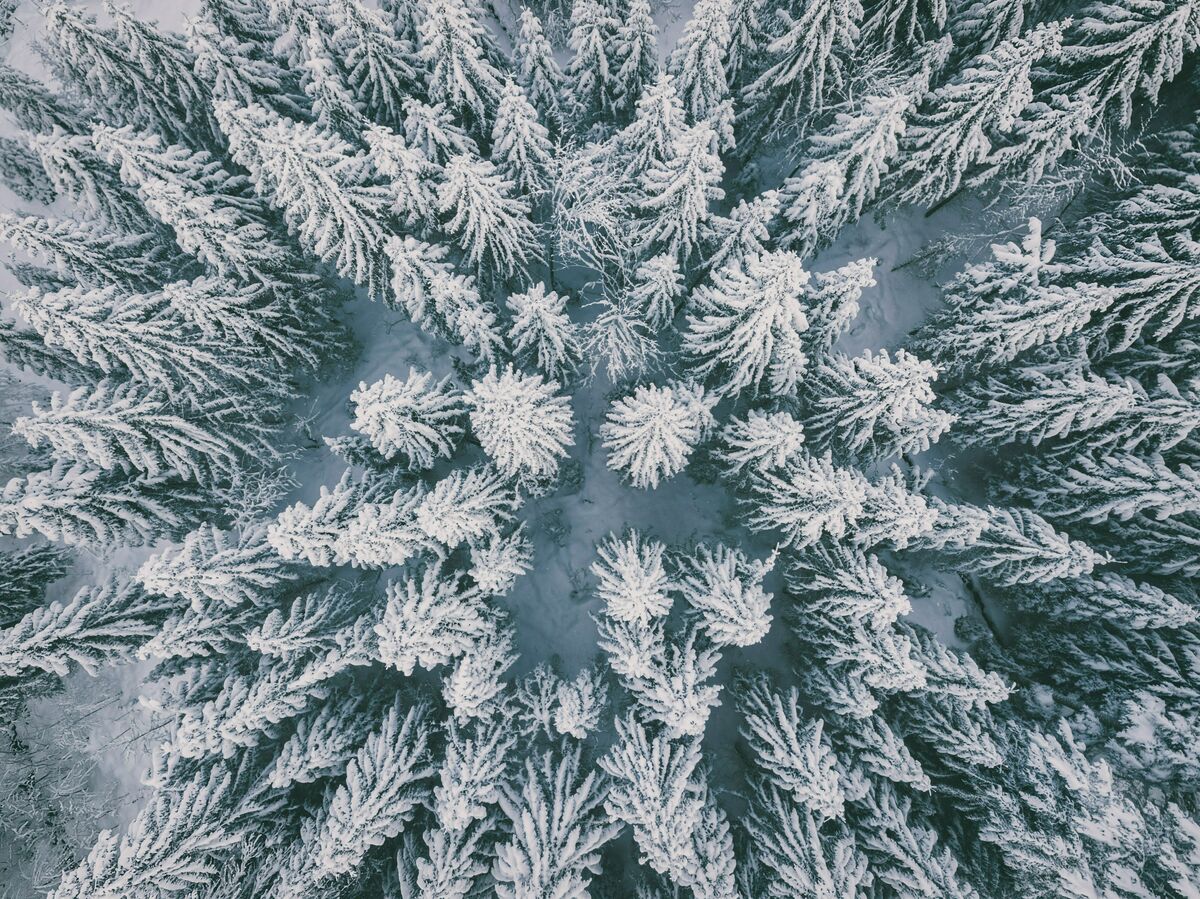
"An idea has become reality, and what has been achieved here is not only technologically impressive, but beyond that, many additional topics were tackled, so that we are really on our way to achieve our goal of creating a comprehensive product for the future."
Horst Rahe